You’ve got a concrete project in the works – exciting! Whether you’re pouring a patio, driveway, or foundation, thorough prep is KEY. Don’t worry, we’ve got your back!
We’ve seen it all. We’ll walk you through everything you need to do to get your property ready for concrete success.
Assess the Installation Area
First things first, take a good look at where you’re putting that concrete. Ask yourself:
- Is the area LEVEL?
- Are there any obstacles like trees, utility lines, or structures in the way?
- How will the concrete be used? (This affects depth and reinforcement needs)
- What’s the soil like? (Clay, sand, etc. require different prep)
Jot down your answers – they’ll guide the rest of your prep process.
Obtain Necessary Permits
Before you break ground, make sure you’re LEGAL. Check with your city or county about permits for concrete work. Trust us, you don’t want to pour a beautiful slab only to have to rip it out because of a paperwork snafu!
Common permits for concrete projects include:
- Building permits
- Zoning permits
- Grading permits
- Right-of-way permits (if your project extends to the street)
Not sure what you need? Give your local building department a call – they’re usually happy to help.
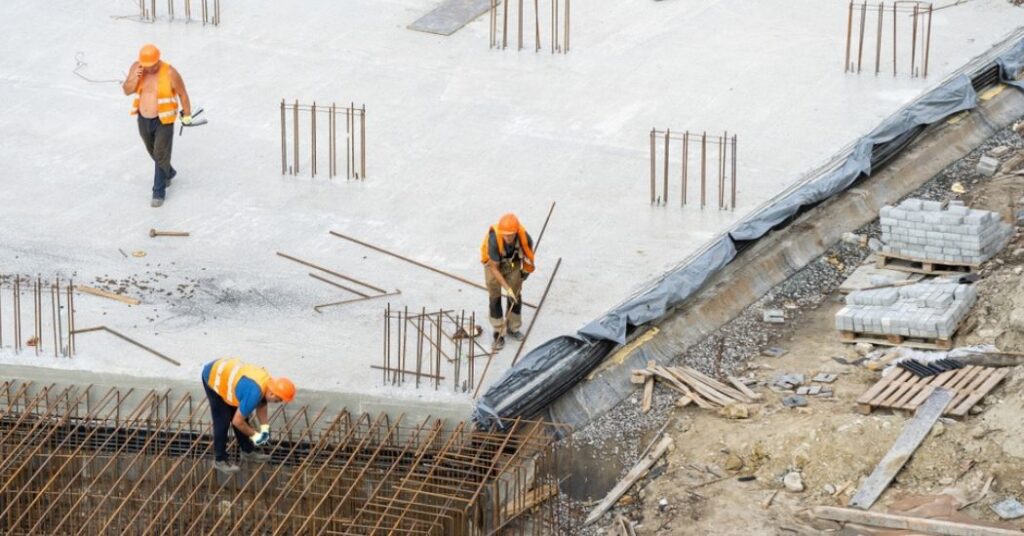
Choose the Right Type of Concrete
One concrete mix does NOT fit all! The right type depends on your project specs like:
- Desired strength
- Exposure to elements (freeze/thaw cycles, salt, etc.)
- Surface finish (smooth, textured, colored, etc.)
- Budget and timeline
We recommend chatting with a concrete pro (like us!) to pick the best mix. A few common options:
- Basic ready-mix concrete
- High-strength concrete
- Fast-setting concrete
- Decorative concrete
- Pervious concrete (allows water drainage)
Measure and Mark the Area Accurately
Now it’s time to map out your masterpiece! Precise measurements are a MUST to ensure your concrete is the right size and shape.
Grab a tape measure, stakes, and string line. Measure the length and width of the area, then use the stakes and string to outline the perimeter. Double and triple check your measurements!
If you’re adding curves or angles, use a garden hose or spray paint to mark those lines. The more accurate your markings, the better your concrete will look.
Clear the Site of Debris
You want your concrete to rest on SOLID ground. That means getting rid of any debris that could interfere with a smooth pour.
Get rid of:
- Rocks and gravel
- Roots and stumps
- Old concrete or asphalt chunks
- Trash and litter
A rake, shovel, and wheelbarrow are your best friends for this step. For bigger jobs, you may need to bring in heavy equipment like a mini-excavator or skid-steer.
Excavate the Area to Required Depth
Time to dig! The depth of your excavation depends on:
- The type of project (patio, driveway, etc.)
- Soil conditions
- Climate (frost depth in cold areas)
- Expected load (vehicles, equipment, etc.)
As a general rule of thumb:
- Patios and sidewalks: 4-8 inches deep
- Driveways: 8-12 inches deep
- Foundations: 18-24 inches deep
Use a shovel or excavator to remove soil to the proper depth. Keep the base of the excavation as level as possible.
Ensure Proper Drainage Around the Site
NOBODY wants a pool of water on their new concrete! Proper drainage is key to avoiding cracks and heaving down the road.
Make sure the area around your excavation slopes AWAY from the site. You may need to add fill dirt to create this slope.
For large areas or poor-draining soil, consider installing a French drain system. This involves digging trenches and laying perforated pipe to direct water away from your concrete.
Install a Stable Sub-base
Think of sub-base as your concrete’s best friend. It’s the foundation that supports your slab, resists settling, and prevents cracks.
Common sub-base materials include:
- Gravel (crushed stone)
- Sand
- Recycled concrete aggregate
Spread your sub-base in 2-inch layers, compacting each layer with a hand tamper or plate compactor. The thickness depends on your project, but 4-6 inches is typical.
Psst…make sure the sub-base extends beyond the edges of your planned concrete. This gives the edges extra support!
Add Forms to Shape the Concrete
It’s time to give your concrete some boundaries! Forms hold the wet concrete in place until it hardens.
You can use:
- Lumber (2x4s, 2x6s, etc.)
- Plywood
- Metal forms
- Plastic forms
Place the forms around the perimeter of your excavation. Make sure they’re straight, level, and STURDY. If the forms move during the pour…yikes! Use stakes, braces, or kickers to keep them in place.
Don’t forget to add form release oil before pouring – this prevents the concrete from sticking to the forms.
Plan for Reinforcement Requirements
Want your concrete to be STRONG like the Hulk? Reinforcement is key! It helps concrete resist cracking, improves impact resistance, and extends the life of your slab.
Common reinforcement options:
- Rebar (steel bars)
- Wire mesh
- Fiber reinforcement (added to the mix)
The type and amount of reinforcement needed depends on your project specs. A structural engineer or concrete pro can help you plan the PERFECT reinforcement setup.
Account for Weather Conditions
Mother Nature can make or break your concrete pour! Heat, cold, rain, and wind all affect how concrete sets and cures.
Here are a few tips:
- Pour concrete when temps are 50-90°F (10-32°C) if possible
- Avoid pouring on SUPER hot, dry days (concrete may dry too fast)
- Don’t pour if there’s rain or snow in the forecast (excess water weakens concrete)
- Use hot water, accelerators, and insulating blankets in cold weather
- Provide shade, cooling tubes, and misting in hot weather
Check the forecast before you pour, and have a plan B if needed!
Ensure Accessibility for Concrete Delivery
Concrete waits for NO ONE! Once the mix is loaded into the truck, the clock is ticking. You’ve got about 90 minutes to get that concrete poured and finished before it starts to set.
Make sure your site is ACCESSIBLE for the concrete truck. Clear a path at least 10 feet wide and 15 feet tall. If the truck can’t get close enough, you may need to use a concrete pump or wheelbarrows to transport the mix.
Talk to your concrete supplier ahead of time to plan the delivery logistics. Trust us, you DON’T want to be scrambling on pour day!
Set Up Tools and Equipment
You’ve got your site prepped and your concrete ordered. Now it’s time to gather your TOOLS! Here’s a checklist:
- Wheelbarrows or carts (for moving concrete)
- Shovels and rakes (for spreading concrete)
- Bull float (for initial screeding)
- Hand floats and trowels (for finishing)
- Edging and grooving tools (for control joints and decorative edges)
- Concrete vibrator (for eliminating air pockets)
- Sprayer or mister (for curing concrete)
Make sure you have EVERYTHING you need before the concrete truck arrives. A well-prepared crew is an efficient crew!
Implement Safety Measures
We know you’re eager to get that concrete poured, but SAFETY should always come first! Concrete work involves heavy materials, caustic substances, and lots of physical labor.
Always:
- Wear gloves, eye protection, and sturdy boots
- Use proper lifting techniques when moving concrete or equipment
- Keep the site CLEAN to avoid trips and falls
- Follow the manufacturer’s instructions when using tools and additives
- Have a first-aid kit on hand (just in case!)
If you’re not CONFIDENT in your ability to work safely, leave it to the pros. No concrete project is worth getting hurt over!
Consider Timing for the Project
Timing is everything when it comes to concrete. You’ve got to coordinate the prep work, delivery, pouring, and finishing to ensure a SMOOTH process.
A few timing tips:
- Start prep work at least a week before your pour date
- Order your concrete at least 48 hours in advance
- Schedule your pour for early morning (cooler temps, more time to finish)
- Allow at least 24 hours for concrete to set before walking on it
- Wait at least 7 days before heavy traffic or equipment on the slab
Remember, RUSHING leads to mistakes. Take your time and do it right the first time!
Inspect the Prepared Site Before Pouring
You’ve done the hard work of prepping your site. Now take a step back and INSPECT your handiwork!
Double-check:
- Forms are straight, level, and secure
- Sub-base is even and well-compacted
- Reinforcement is properly placed and tied
- Site is clean and free of debris
- Tools and materials are staged and ready to go
If everything looks good, give yourself a pat on the back – you’re READY TO POUR!
Final Thoughts on Preparation
We’ve covered a LOT of ground in this guide to prepping your property for concrete. From permits and planning to excavation and forming, there are MANY steps involved in setting the stage for a successful pour.
The KEY TAKEAWAY? Proper preparation is ESSENTIAL. Skimping on prep work can lead to a host of problems down the road – cracks, settling, drainage issues, you name it.
At Boise Concrete Contractor, we’ve seen the GOOD, the BAD, and the UGLY when it comes to concrete prep. Trust us, it pays to do it RIGHT the first time!
If you’re feeling overwhelmed or unsure about any part of the prep process, don’t hesitate to call in the PROS. We’re here to help you achieve the concrete project of your DREAMS!
FAQs
What permits are needed for concrete projects?
Required permits vary by location and project type. Common ones include building permits, zoning permits, grading permits, and right-of-way permits. Always check with your local building department to see what’s required in YOUR area.
How deep should the excavation be for concrete?
Excavation depth depends on the type of project, soil conditions, climate, and expected load. As a general rule, plan on:
- 4-8 inches for patios and sidewalks
- 8-12 inches for driveways
- 18-24 inches for foundations
When in doubt, DEEPER is better for stability and frost protection.
What types of concrete are available for different projects?
There are MANY types of concrete mixes, each with its own strengths and uses. Some common options:
- Basic ready-mix (versatile, affordable)
- High-strength (for heavy loads and harsh conditions)
- Fast-setting (when you need it to cure QUICKLY)
- Decorative (colored, textured, or stamped for aesthetics)
- Pervious (allows water to drain through)
Talk to your concrete supplier or contractor to choose the BEST mix for your project.
How can I ensure proper drainage?
Proper drainage is KEY to avoiding pooling water and premature cracks in your concrete. Make sure the area around your concrete slopes AWAY from the slab. You may need to add fill dirt to create this slope.
For poor-draining soils or large areas, consider installing a French drain system. This involves digging trenches and laying perforated pipe to direct water AWAY from your concrete.
What safety measures should I consider during the project?
Concrete work can be DANGEROUS if you’re not careful! Always wear proper safety gear (gloves, eye protection, sturdy boots). Use proper lifting techniques when moving heavy materials. Keep the site clean and tidy to avoid trips and falls.
If you’re working with tools or additives, FOLLOW the manufacturer’s instructions to the letter. And ALWAYS keep a first-aid kit on hand, just in case.
Remember, NO concrete project is worth risking your safety over. If you’re ever unsure, play it SAFE and call in the professionals!